Pultrusion, a manufacturing process for producing continuous length composite materials is becoming increasingly popular in various industrial applications. Unlike other manufacturing processes, pultrusion is cost-effective in producing high volume production runs of constant cross-sectional parts for various industries. One of the major advantages of this process is its ability to manufacture custom profiles and standard shapes that can be adapted to increase versatility in industrial applications.
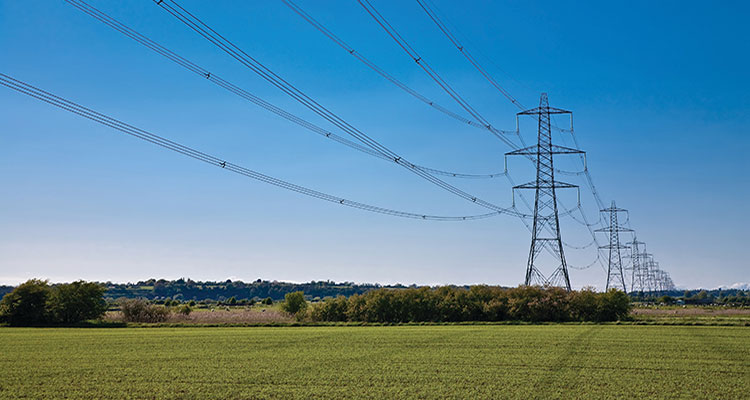
Pultrusion is a continuous process that involves the processing of reinforced fibers and resin systems, which are fed into a heated steel mold. The reinforcement fibers are pulled through the mold, where they are impregnated with liquid resin systems, and then cured to form the finished product. This process of pulling the reinforcement fibers through the mold is what gives the finished pultruded part its continuous, uniform, and strong properties.
This process is versatile and can be applied to a wide range of composite materials of varying sizes and shapes. The most commonly produced materials include fiberglass pultrusions, as they lend themselves naturally to the pultrusion process. Also, composite materials such as carbon fiber, aramid, natural fibers, and other materials have been successfully pultruded as well.
One of the most notable applications of pultruded composites is in the production of pultrusion gratings. Pultruded gratings are used in a variety of industrial applications requiring high strength, durability, and resistance to harsh environments. The use of pultruded gratings is commonly seen in industrial plants, offshore oil rigs, marine facilities, wastewater treatment plants, and other corrosive environments.
The primary advantages of pultruded gratings are that they are lightweight, durable, and require minimal maintenance. They also provide an excellent alternative to traditional materials such as steel, aluminum, and wood. Pultruded gratings are available in various sizes, shapes, and thicknesses, making them versatile and adaptable to various applications.
Another application of pultruded composites is in the production of custom profiles and standard shapes. This process has made it possible for industries to manufacture complex shapes and sizes that are suitable for their specific applications. These custom profiles and standard shapes are used in various industries such as automotive, aerospace, construction, and others.
Pultrusion provides a cost-effective, reliable, and efficient manufacturing process for producing composite materials. The ability to produce high-quality parts in high volumes, coupled with the flexibility to produce custom profiles and standard shapes, make pultrusion a preferred method of manufacturing for various industries.
In conclusion, pultrusion has become an increasingly popular method of producing continuous length composite materials that are strong, durable, and cost-effective. The process has made it possible for industries to manufacture custom profiles and standard shapes, which have opened up new applications in various sectors. The versatility of pultrusion allows for the production of different composite materials making it an indispensable asset to various industries. Pultrusion Gratings, Fiberglass Pultrusions, Composite Materials, and Industrial Applications are some of the crucial areas where the process has found widespread application.